NinoTNC N9600A3 Assembly
page modified October 5, 2020
Specifications may change without notice.
Do not use this device in any situation where loss of life or property would be the result of the device missbehaving or failing.
If you go beyond this rule, you are self certifying this device.
This device is built by hobbyists for a hobby project.
We do not certify that this design, or any particular unit, is sound.
Use at your own risk.
Feel free to use these 3 images for publicity or articles!
These are the assembly instructions for the N9600A3 board. Make sure the silkscreen information on the board you are assembling matches this.
The bill of materials linked below is specific to the N9600A3 board, both with and without the 'r3' mark.
There are some instructions specific to the 'r3' and others for the prior 'r2' boards.
Only the 'r3' board is specifically marked.
The differences between the two boards are in the installation of resistor R12 in step 7, and jumper J6 in step 20.
Additionally capacitor C12 is in a different location in step 9.
|
|
First Time Kit Builders
People who are unfamiliar with kit building may approach this as their first kit but there are a few caveats.
- Be careful. While this kit is one of the easier and better documented kits, and building a kit is pretty easy,
a cavalier attitude will result in hard-to-diagnose failures.
-
Have an experienced hand available for guidance and troubleshooting.
Building a kit is much easier than fixing a kit.
It is possible to reverse a soldering mistake, but it is definitely much harder than doing it right the first time.
If you have any doubts, send a message to [email protected] and we'll try to help you out.
-
If you find anything in the instructions which is unclear, write us.
We'll try to fix it.
-
If you are a first time kit builder, please consult your local experienced builder for help in reversing any mistake.
-
#4 is important.
-
Adafruit
has some excellent tutorials on soldering.
Buy the parts from Digikey
Here's how to do it.
Bill Of Materials
|
Right-click on this link and save the n9600a3 bom csv file to your computer.
This is the Digikey shopping list for the TNC.
Find the n9600a3 csv file on your computer (it will be named starting with n9600a3 and will be a csv, comma separated values, file)
|
|
Go to Digikey website
|
Click on this link: Digikey
|
|
Shopping Cart
|
Click on the shopping cart.
If presented, click on View Cart button.
|
|
New Cart
|
if there is no New Cart button, skip to Upload CSV, else click the New Cart button.
|
|
Upload CSV
|
There is an Upload A File field in the middle of the form.
Drag the CSV file from your Finder/Explorer into that field, or click on the Browse link, and then navigate to the CSV file.
|
|
Confirm Mapping
|
You will see a pop-up window titled "Upload File Mapping".
Find the titles (in row 1) on that window and make sure the column headers match the text in the title row.
Make sure the third column ROW drop-down says "Customer Reference".
Click on Add To New Cart
|
|
USB cable?
|
If you need a USB A male to USB B male cable, add it now.
Part# WM21039-ND is $2.16 for a 3'4" cable.
There are suppliers of 1 foot USB-B cables at other vendors (Amazon).
Short is better for RF immunity but it does have to make it from the host computer (Raspberry Pi) to the NinoTNC.
|
|
Checkout
|
Inspect the list. If anything is backordered, stop and send an email to [email protected] email reflector.
Almost everything is available from a second source right on Digikey. We'll fix it and send a reply.
If you go ahead and let it be backorded, DigiKey will charge you postage twice.
Now do checkout and pay for your order.
Shipping: USPS shipping is the cheapest.
Paypal works.
|
|
What if you already have A2 parts unused?
If you already have a stash of A2 parts, then you can just supplement your stash with the
- 22K resistor,
- 180ohm resistor,
- 47K x 5 resistor array,
- 4N25 opto-isolator,
- MCP2221A USB bridge,
- 4-bit DIP switch,
- 2-pin header,
- 2-pin jumper,
- USB-B connector,
- USB-B cable,
Download this BOM (Bill Of Materials) of 10 parts, including USB-B cable, and order it via the above instructions.
This will cost you about $8+shipping if you need the USB-B cable, or about $6+shipping if you do not.
If something is backordered, send a message to
[email protected] and we'll get it straghtened out.
Assembly Instructions
What you will need
- Volt Ohm Meter
- Wal-wart or current protected power source. Don't use a PC or expensive non-protected source to power the board until after the NinoTNC passes the regulator test.
- Clip-lead with clips on both ends for use in testing
- Magnifying glass or smart-phone with close-up zoom capability
- Solder sucker (DS017 Soldapult for instance)
- Thin rosin core solder - 0.02inch to 0.04inch - 0.5mm to 1mm. Kester 0.02inch Solder
- Soldering iron with thin tip - I use a Weller temperature controlled soldering station at 650 degrees.
This is the good soldering station at $120. Weller soldering station
This one’s probably good too at $45. Far East brand soldering station
- Computer capable of supporting a KISS TNC connected via USB
- Radio wired for KPC-3, TNC-PI or NinoTNC 9 pin D-sub connector
⇒ All parts are inserted from the silk-screened side of the board, i.e. from the side on which the white writing is printed.
|
⇒ Except where specifically noted, all two pin components are non-polorized so you can put the part onto the board with the pins in either hole.
|
Soldering tips
Insert the component so it is flush without breaking the part.
Splay the wires out to keep the part in the board while you invert it to solder.
Solder the part.
Inspect the leads to make sure the solder comes up over the lead for a visible amount.
Cut the lead at the wire, not the solder.
The solder is your friend.
What you do NOT want is a lead which is not making good electrical contact with the hole.
When debugging the board because something went wrong, it is nice to have a clear image of the naked board. Here you go:
A3 rev r2 board:
Click either to enlarge
A3 rev r3 board:
Click to enlarge
Here's the A3 rev r2 PCB's schematic. Click to load the PDF.
Some of the images on this page can be enlarged and opened in a new browser tab by clicking on them.
Install parts in this order:
1 |
Y1 |
7.3728 MHz crystal
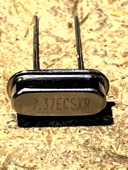 |
The crystal will have some lettering on it containing the numbers 7.37
The crystal and two capacitors form an oscillator to provide clocking for the CPU's digital circuits.
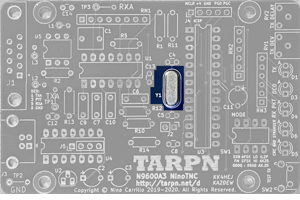 |
2 |
R11 |
47 kΩ 5% 1/4 W resistor
|
R11 turns off the MCLR input to the CPU.
|
3 |
R5 |
8.2 kΩ 5% 1/4 W resistor
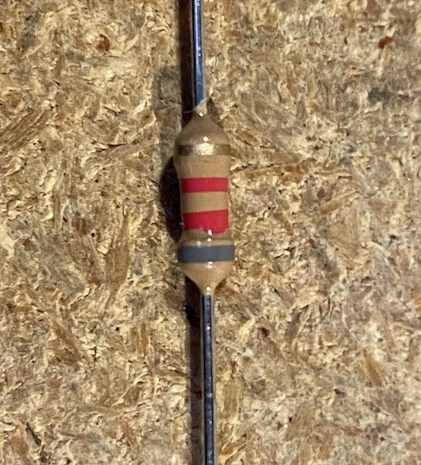 |
In the TX-data/audio path between U1B and U1C op amp devices.
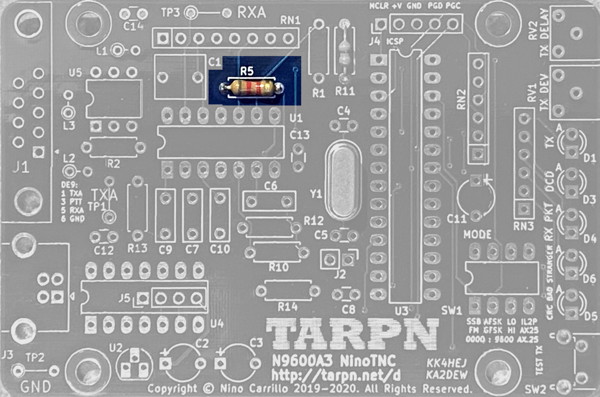 |
4 |
R1 |
470 Ω 5% 1/4 W resistor 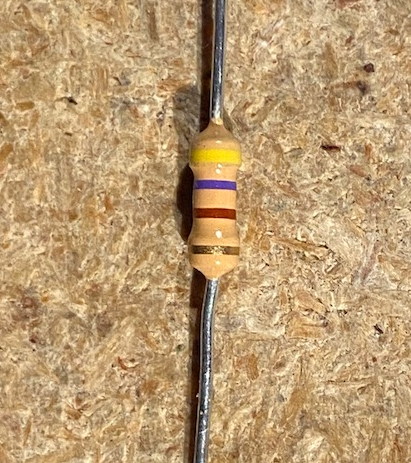 |
This is a low-end-limit to the Deviation adjust.
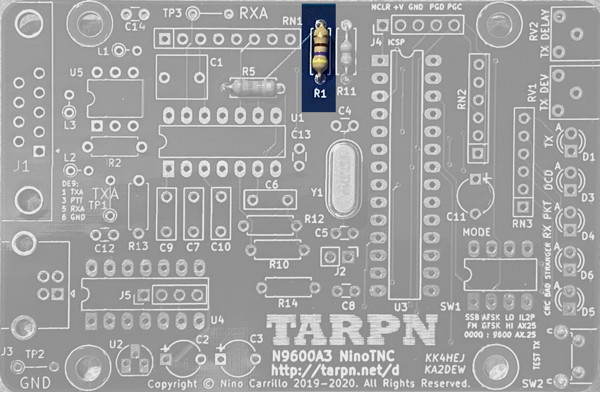 |
Note: the color codes on the 1% resistors are pretty hard to use.
If you are receiving your resistors in a mixed bag of parts, you probably want to do all of steps 5, 6, 7, and 8 before soldering the resistors so you
can double check the color codes before you solder and cut.
I recommend using a VOM to prove that R14 and R13 are what you think they are, and not one of the other ones.
5 |
R14 |
14.7 kΩ 1% 1/4 W resistor 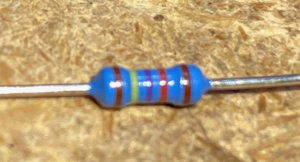 |
This is part of the amplifier circuit for the 1st op-amp stage in the transmit data circuit.
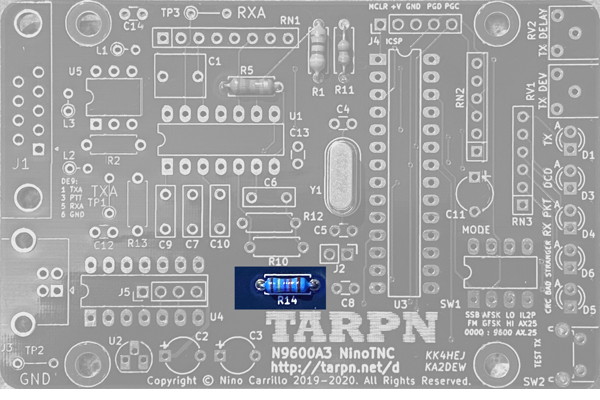 |
6 |
R13 |
7.15 kΩ 1% 1/4 W resistor  |
This resistor is in the input and feedback loop for the 1st op-amp stage in the TX-data/audio path.
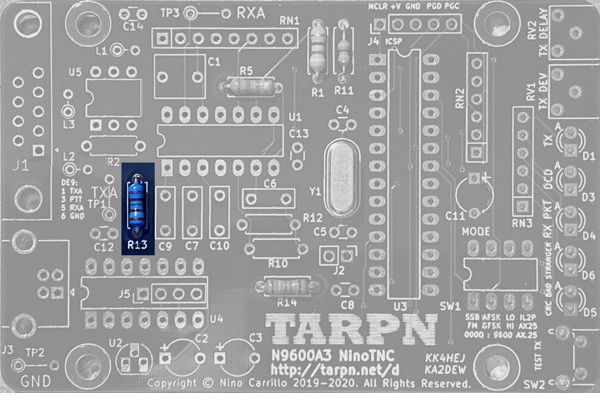 |
7 |
R12 |
4.75 kΩ 1% 1/4 W resistor 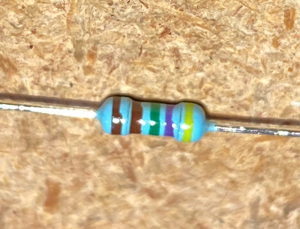 |
This resistor is in the audio path between the 1st and 2nd op-amp stage in the TX-data/audio path.
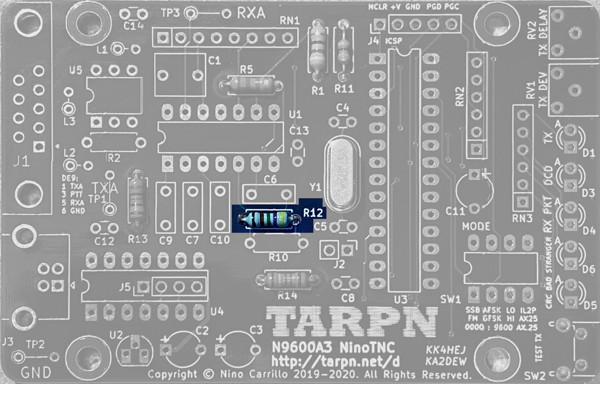 |
8 |
R10 |
7.87 kΩ 1% 1/4 W resistor 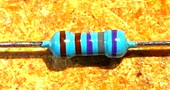 |
This resistor is in the input and feedback loop for the 2nd op-amp stage in the TX-data/audio path.
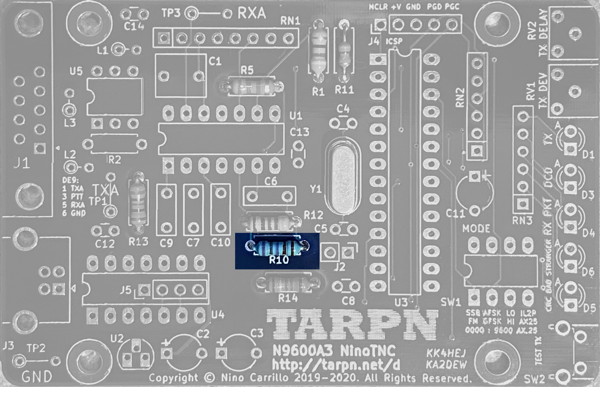 |
9 |
C8, C12, C13, C14 |
0.1 µF 10% 50 V Ceramic capacitor 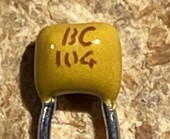 |
These ceramic radial capacitors provide power supply filtering and glitch reduction on the CPU’s main power input and at 3 other places around the board. .
Note: C12 is half an inch to the right of where pictured for boards marked with 'r3'.
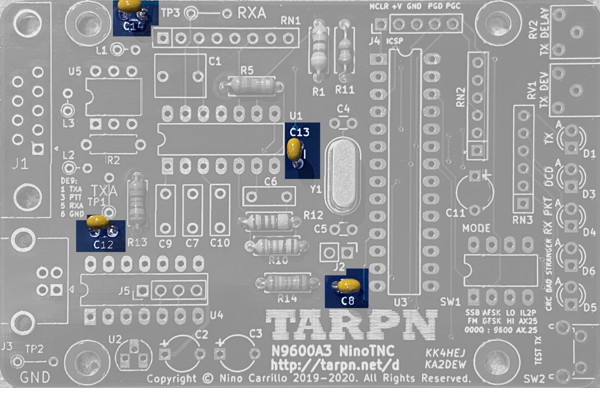 |
|
|
|
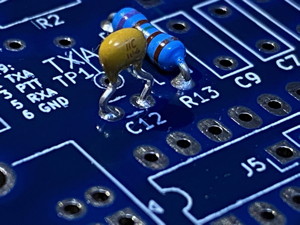 |
10 |
C4 and C5 |
18 pF 5% 50 V Ceramic capacitor (may be 100 V) 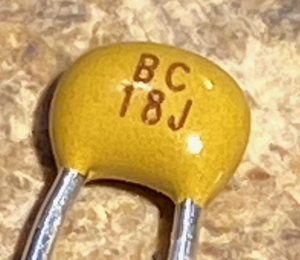 |
C4 and C5 are part of the crystal oscillator circuit
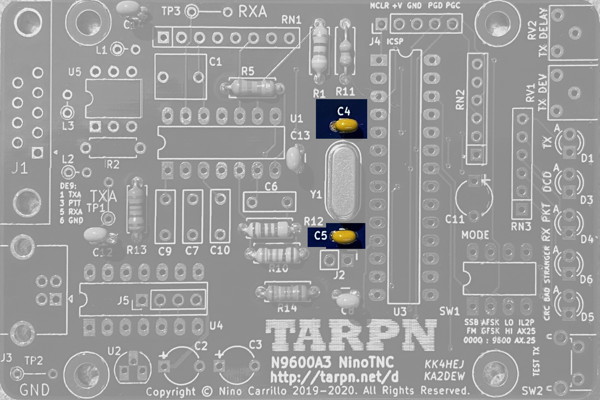 |
11 |
R2 |
180 Ω 5% 1/8th W resistor 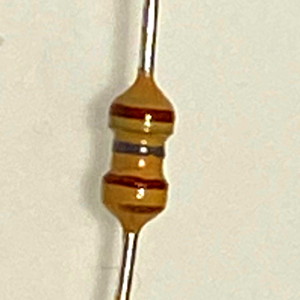 |
R2 is the current limit resistor between the GPIO and U5, optoisolator.
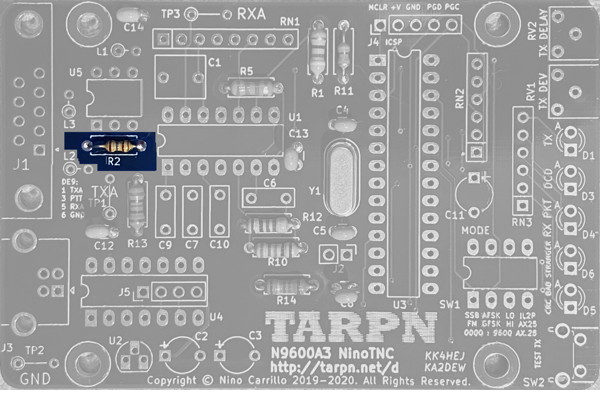 |
13 |
U5 |
4N25 iso-optilator PTT driver.
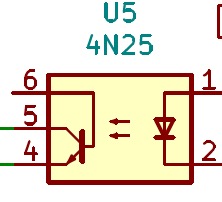 |
Install so the pin 1 dot on top of the part is toward the half-moon on the PCB.
This six-pin device is driven by a GPIO on the CPU and is responsible for pulling the PTT line to ground when the NinoTNC wants to send a packet.
If this part is missing, dead, or inserted incorrectly, the TX LED on the TNC will still light, but the radio will not transmit.
An opto-isolator uses an internal light source to charge the optically sensitive diode which allows energy to pass.
This sealed package performs the duties of an open collector transistor but with a major feature that no energy at the collector can pass back to the gate/base.
Consult the schematic diagram. Pin 6 is left disconnected. Pin 3 is a no-connect.
Pin 1 is driven by the CPU pin 4 GPIO through a 180 Ω resistor R2. Pin 2 and 4 are tied to ground.
When P1 is raised high, the internal LED illuminates the transistor between pins 4, 5, and 6, causing pin 5 to pull to near ground, keying up the attached radio.
In a traditional TNC, the CPU drives the transistor through a resistor but if the transistor is not driven, the PTT pull-up voltage at the transmitter can leak back through.
This is of no consequence if the CPU is powered up.
However, if the CPU is powered off, and the radio is on, the radio can actually provide enough energy leaking through the PTT circuit to activate the CPU.
The CPU will then start its boot up procedure, possibly reading control inputs (which are powered down) incorrectly.
The opto-isolator prevents the PTT leakage from getting to the CPU because there is no route backwards through the LED.
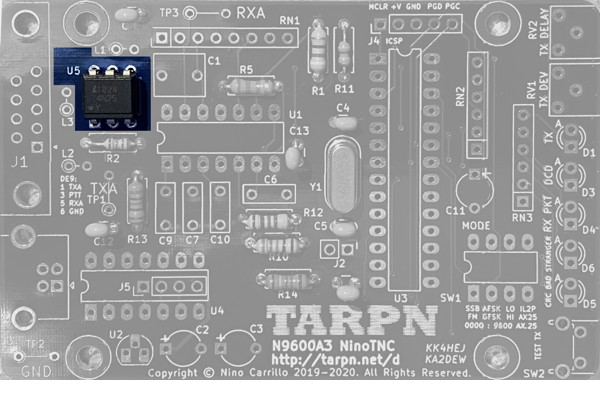 |
| | 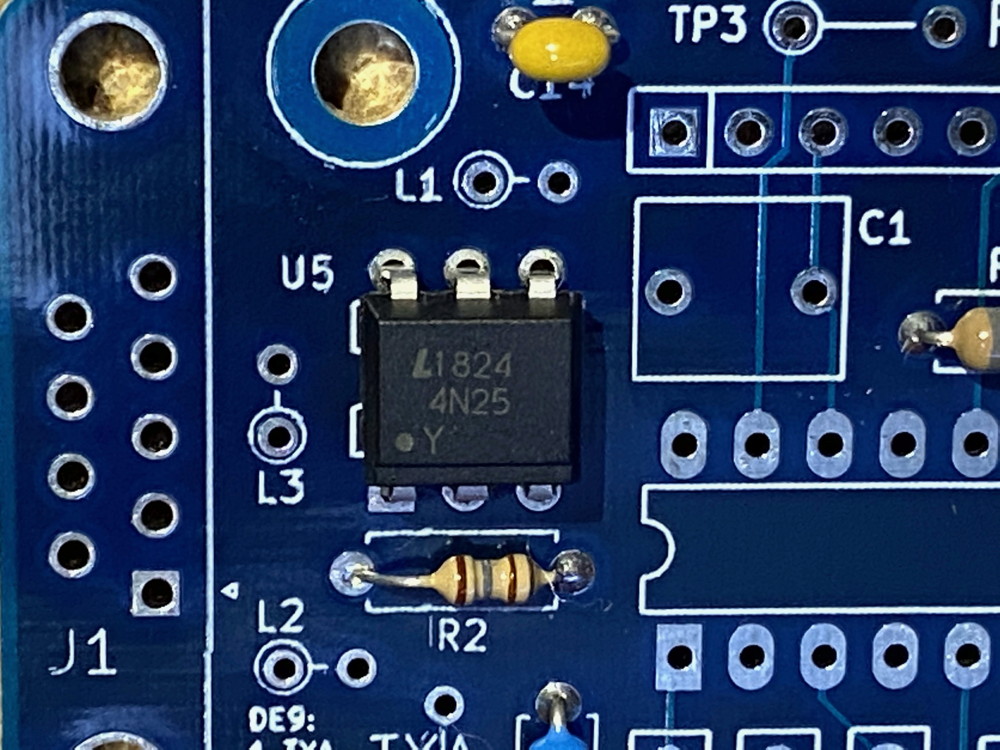 |
14 |
XU3 |
28 pin DIP IC socket for U3
| This is the socket for the CPU.
- Make sure all pins are straight before you insert the socket.
- Use long-nose plier to fix any that need fixing.
- Carefully insert into the board with the round half-moon end pointing to match the board. -- That will be up from the perspective of this image.
- Once all 28 pins are showing through the board, bend the corner leads outward to keep the socket from falling out as you invert the board to solder.
|
15 |
U2 |
MCP1702 3.3 V 250 mA TO92 case regulator 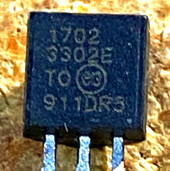 |
This part takes the 5 V DC from the USB connector and regulates it down to 3.3 V, as needed by the CPU.
Align flat edge with the board silkscreen
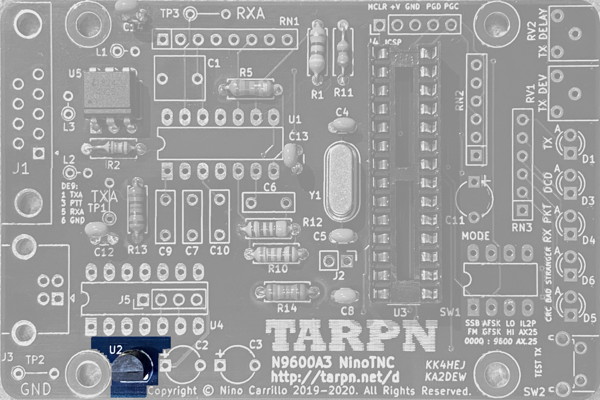 |
16 |
RN1 |
4 resistor resistor network.
Could be 56 kΩ or 100 kΩ
Note: Text on the part itself could be different because 56 kΩ or 100 kΩ is suitable. |
Orientation is important!
Pin 1 is identified by the square around the hole on the PCB and an interesting symbol near the end pin on the component.
See schematic symbol below. If you are looking at the print on the one side of the resistor pack such that the pins are down, then pin1 is on the left.
This part serves as a pair of resistor voltage dividers. The first follows the input audio coupling capacitor so the voltage of the RX audio is centered around 3.3v/2.
The second is used to provide a bias to the C element of the MPC6004 quad op-amp package in the final stage of the TX audio shaping.
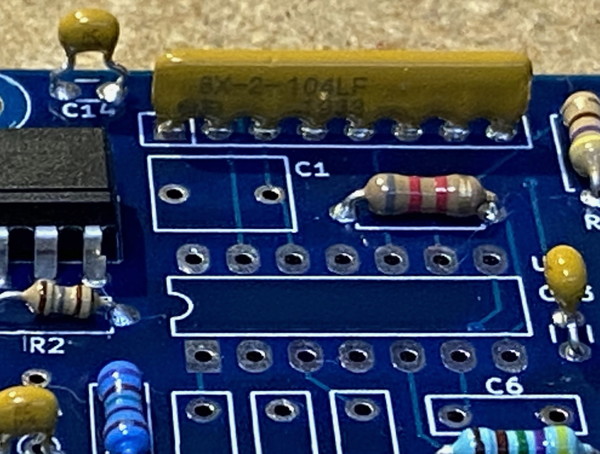 |
Be Careful here. The next two steps install resistor packs which are the same shape and size!
17 |
RN2 |
5 resistor 47 kΩ resistor network
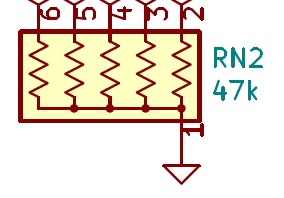 |
Orientation is important!
Pin 1 is identified by the square around the hole on the PCB and an interesting symbol near the end pin on the component.
See the prior RN1 step.
See schematic symbol below.
This provides pull-ups for chip ID and the dip-switch
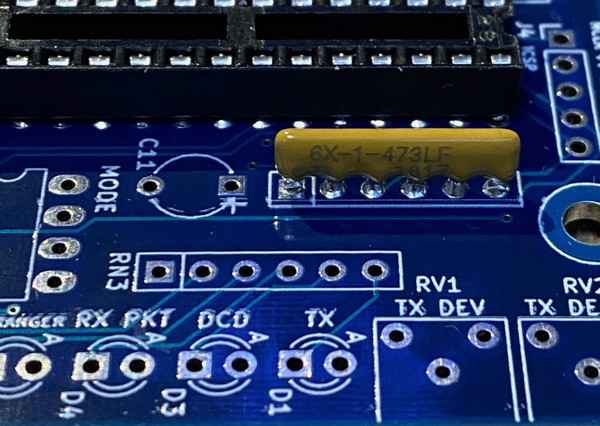 |
18 |
RN3 |
5 resistor 180 Ω resistor network
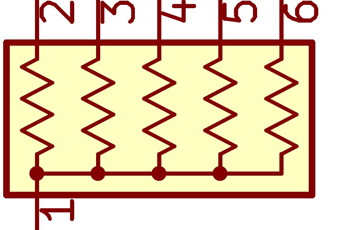 |
Orientation is important!
Pin 1 is identified by the square around the hole on the PCB and an interesting symbol near the end pin on the component.
See the prior RN1 step.
See schematic symbol below.
This provides an in circuit resistance to limit the LED current for 5 LEDs
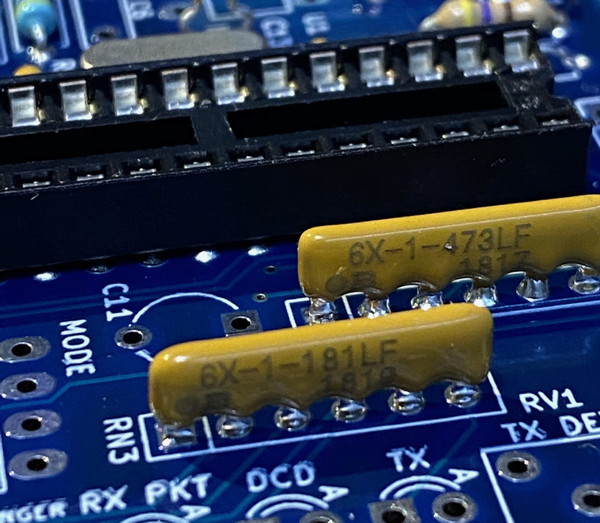 |
19 |
SW1 |
4 position dip-switch 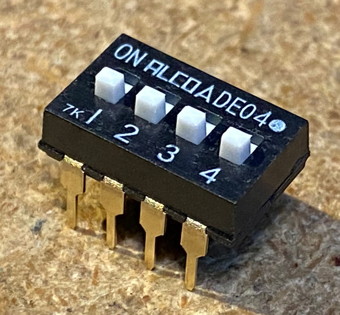 |
Install the switch so the label 1 2 3 4 is toward the TARPN label side of the board.
Each switch is a separate circuit.
These switches, and the 47K pull-down resistors in resistor package RN2, drive four separate inputs on the CPU to select options.
If the switch is closed (toward the resistor packages), the switch puts VCC into the CPU's GPIO input.
If the switch is open (toward the TARPN logo), the resistor pack RN2 resistors pull the GPIO to ground.
|
step #20 is only for boards marked with 'r3' next to the lower-left screw-hole
This step is new for the June shipment of A3 boards.
I originally put this step in as a last step but it turned out to be nearly impossible to solder this part in after all of the really tall parts were already installed.
So.. I renumbered all of the steps after step 20. I hope this doesn't cause unrest.
20 |
J6 |
2 pin jumper
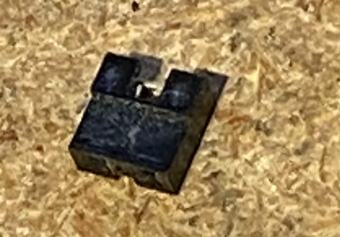 |
This jumper bypasses R3 on the output of the tranmit audio circuit.
In your kit is a plastic widget (called a 'shunt') which covers and shorts out this jumper position.
See picture.
Note that the J6 shunt could be white, red, blue or black.
If the J6 shunt is - installed, then the NinoTNC will output a louder transmit audio signal, appropriate for the data connector on 9600-capable radios.
If the shunt is
- removed, the output signal is reduced, suitable for microphone inputs.
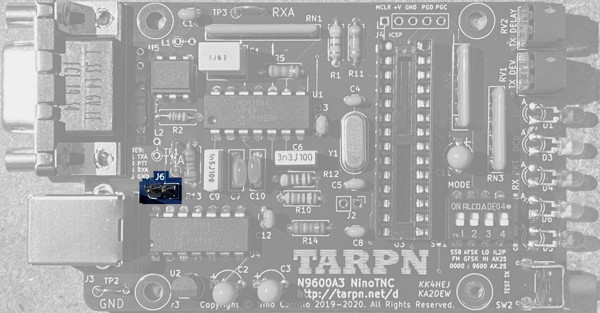 |
21 |
C6 |
3300 pF [metal] film capacitor radial leads
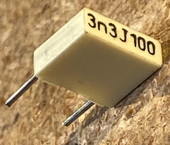 |
This is part of the feedback loop in the 2nd stage of the transmit data output.
|
22 |
C9 |
1500 pF [metal] film capacitor radial leads
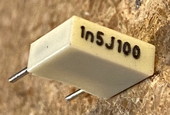 |
This is part of the feedback loop in the 1st stage of the transmit data output.
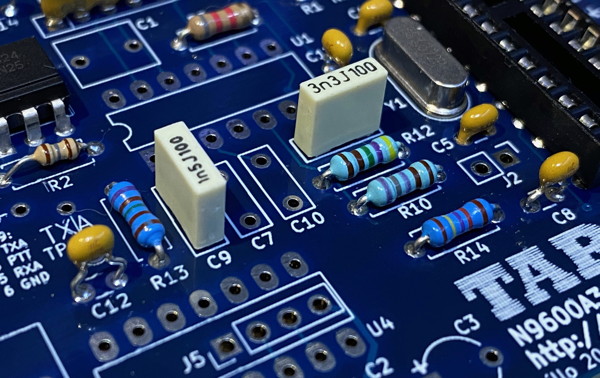 |
23 |
C1 |
1 µF [metal] film capacitor radial leads
or
|
This is the capacitive coupling immediately following the DE9 receive data input, before the op-amp receive buffer.
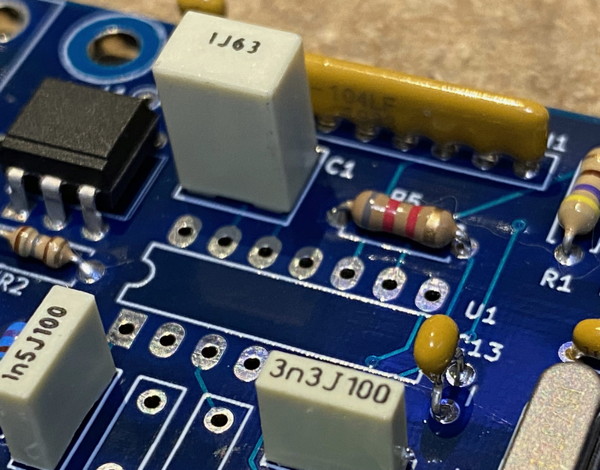 |
24 |
C2, C3, C11 |
10 µF 10% 16 V tantalum dipped capacitor
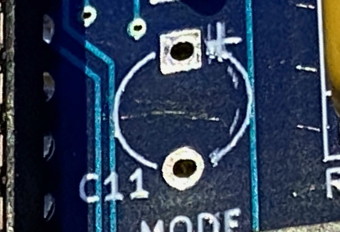 |
Carefully observe values and polarities.
Positive side is marked with a very small plus sign on the part, or a red stripe, and goes into the square solder pad/hole on the PCB.
The silk-screen actually has a microscopic + sign.
C2 is 5v filter on the input to the regulator.
C3 is the 3.3v filter on the output from the regulator.
C11 is vcap input to the CPU on one side and ground on the other.
|
25 |
RV1 |
10 kΩ 1/2 W cermet 1-turn side adjusted trimmer potentiometer. Label="103" 10 * 10**3 = 10000 Ω.
Notice the arrow on one of the legs of the yellow cross. It is pointing down in this image. |
Place in holes so screwdriver adjustable part faces the edge of the board.
This adjusts the Tx Audio level
|
26 |
RV2 |
10 kΩ or 100 kΩ 1/2 W cermet
1-turn side adjusted
trimmer potentiometer.
Label="104"
10 * 10**4 = 100000 Ω
or "103"
10 * 10**3 = 10000 Ω.
Notice the arrow on one of the legs of the yellow cross. It is pointing down in this image. |
Place in holes so screwdriver adjustable part faces the edge of the board.
This unit adjusts the TXDELAY.
The potentiometer selects a voltage between ground and 3.3 V which is passed to an Analog-to-Digital converter pin on the CPU.
The resistance of the potentiometer is less important than that the pointer selects a voltage between 0 and 3.3v.
A higher value potentiometer would have less leakage between the 3.3 V power supply through the part to ground.
But even a 10 kΩ pot only has .33 Milliamps of flow.
The potentiometer is read by an AtoD port on the CPU which figures out how much delay between PTT and starting the packet based on the AtoD reading it gets.
<
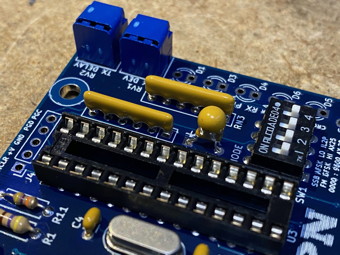 |
27 |
C7, C10 |
1200 pF 50v capacitor
light-yellow polyester-film
or blue ceramic
|
In the transmit Op Amp chain, these two capacitors are across the input on each of the first two stages.
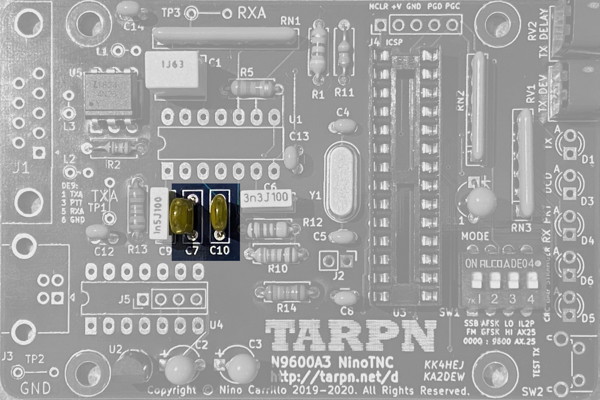 |
28 |
J3 |
USB-B socket
|
This socket has 6 solder points, two of which look like they'll get in the way when you insert them. They don't.
But they will hold this connector onto the PCB.
Solder all 4 pins and the 2 support items.
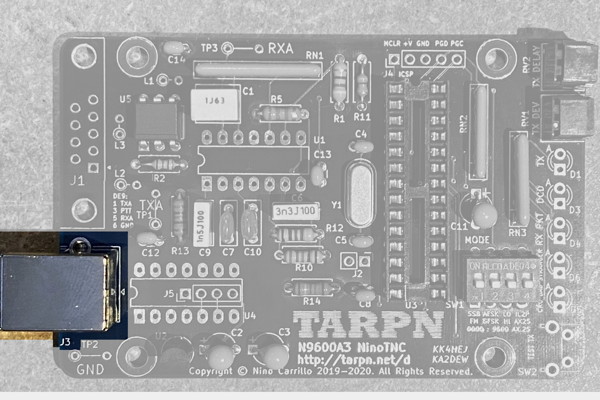 |
Test #1 -- Regulator Test
Now that the USB connector is on the board, 5 V will get to the board. It will be regulated down to 3.3 V by U2 and will show up at the CPU socket at pins 27 and 28.
Test procedure:- Hook the TNC USB up to a robust USB power source.
Don't use a PC or expensive non-protected source until after the NinoTNC passes the regulator test.
A soldering error could lead to shorting out your workstation.
Use a wall wart at this step.
- Use VOM set to DC at a 5-volt-or-more scale and check for 3.3 V at pins 27 and 28 of the 28-pin connector.
- These are the two pins in the upper right of the socket, or closest to the RV2 potentiometer. See the photo.
- Observe something between 3.25 and 3.35 volts on the display.
- Don't worry about the polarity, only the voltage.
If this test fails, inspect the USB connector, U2, C2, C3, socket U3. Also look for any solder bridges (smudge between two solder points) or insufficient solder on a pin.

29 |
SW2 |
side facing push button switch labelled TEST TX
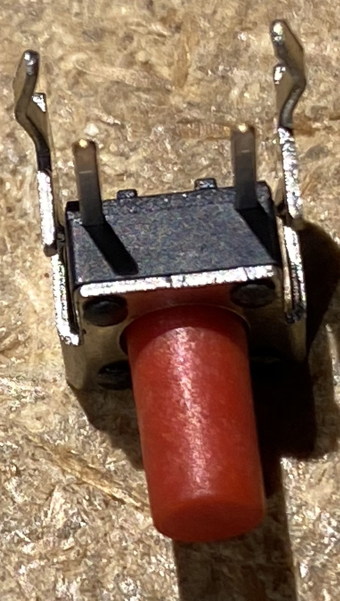 |
Mount so switch button faces off the edge of the board, directly away from the J3-pins in step 24.
Pressing this button connects a GPIO input on the CPU to VCC.
Releasing lets the GPIO be pulled to ground through RN2 47 kΩ pull-down resistor.
This switch will tell the NinoTNC to transmit a calibrated tone.
|
In the next steps you'll be soldering 5 LEDs onto the PCB.
When you cut the leads, save the trimmings for use as scope test loop wire in a later step.
You only need 3 longish thick wire leads for the scope test loops, but
save as many as you can for practice purposes.
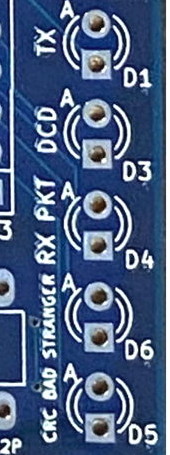 |
D1 |
LED Red diffused
 |
TX - This LED is illuminated when the NinoTNC is keying the radio through the opto-isolator. |
D3 |
LED Yellow diffused
 |
Data Carrier Detect.
This LED will illuminate during radio received when several zero crossings occur in the wave-form (noise) which match the selected bit rate. |
D4 |
LED Green Diffused
 |
Last RX packet was decoded properly.
This LED remains illuminated until the next receive packet starts, even if the TNC transmits several times before then. |
D6 |
LED Orange Diffused
 |
This LED was the Stranger LED in firmware 2.44 and older.
It becomes the Pending LED in firmware 2.45 and newer.
This Stranger LED illuminated when a packet is decoded with a sender callsign which does not match any of the callsigns called by this TNC.
The Pending LED illuminates when the TNC has a message ready to transmit but hasn't had the opportunity to get rid of it yet. |
D5 |
LED Red diffused |
CRC error on receive packet,
This LED illuminates when a valid callsign field is received but the checksum/CRC on the packet doesn't match the rest of the packet and error correction either couldn't be applied, or didn't fix the problem. |
31 |
U3 |
Microchip dsPIC33EP256GP502 CPU
The CPU delivered from ETSY is programmed with released firmware and is ready to be a USB TNC.
No reprogramming required for all supported modes.
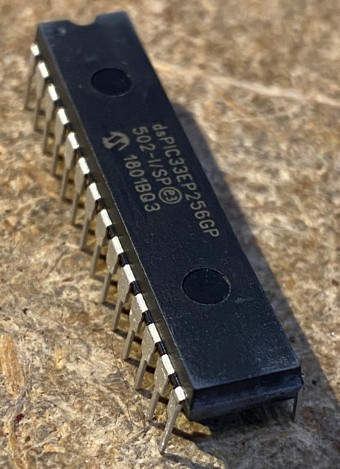 |
To make the chip fit into the socket easily, place the leads on one side against a hard flat surface and push on the package to bend the leads.
Then turn the IC over and do the same thing on the other side.
The pins themselves should be straight, but not splayed out like they are when the IC shipped.
Make sure the half moon on the IC matches the half moon on the socket and on the PCB.
|
Test #2 -- CPU Clock, LEDs, and TEST TX Button
Test procedure:- Attach USB-A to USB-B cable to a powered USB-A socket.
- Plug the USB-B plug into the NinoTNC and observe the LEDs.
The yellow DCD LED should illuminate for a fraction of a second and then go out, at which point the Green RX PKT LED should illuminate and go out.
Orange LED should follow and then Red CRC-BAD LED.
The sequence then reverses until the DCD LED lights and goes out.
- Switching any of the 3 dip-switches closest to the LEDs will cause the LED sequence to repeat.
- Push the TEST TX button and observe that the TX light illuminates. With 2,45 and later firmware versions the Orange light and TX light will illuminate together when the TEST TX button is pressed.
If all 5 LEDs were made to illuminate, and if the three dip switches caused the LED cycle to repeat, skip to the next step.
You are done with LEDs.
If the LEDs did not perform as described, check the CPU for bent pins.
Failing that, inspect the LEDs carefully.
The tops of the LEDs should look like this: Back like this:

Closeup of top of silkscreen side of PCB with LED. Notice the shape of the metal inside the bulb.
Closeup of top of back side of PCB with LED. See here that there appears to be a slot between metal pieces inside the bulb.
Now check the photos up above and see if you can tell that the LEDs match on the top photo and on the back photo.
If your inspection shows the LEDs are installed correctly, reapply power and use your VOM to measure the DC voltage of pins 27 and 28 of the CPU.
These are the pins closest to RV2 potentiometer in the corner of the board.
You should see 3.3 V.
If not, check for shorts or badly inserted pins on the CPU.
If you do see 3.3 V, we have a problem that might take an oscilloscope to check.
Try swapping CPUs with another board if one is available.
Even a CPU from an A2 board would at least light the LEDs.
Look for 7.3mhz sine wave on pin 9 and 10 of the CPU.
If 7.3Mhz is present, then its possible your CPU is not programmed.
32 |
Test points TP1, TP2, TP3 |
These are loops of scrap wire bent around the blade of a long-nose-plier.
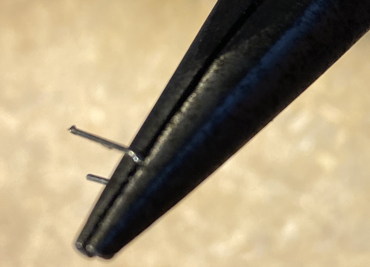 |
Test points for receive audio, transmit audio and ground.
See pix below for installation.
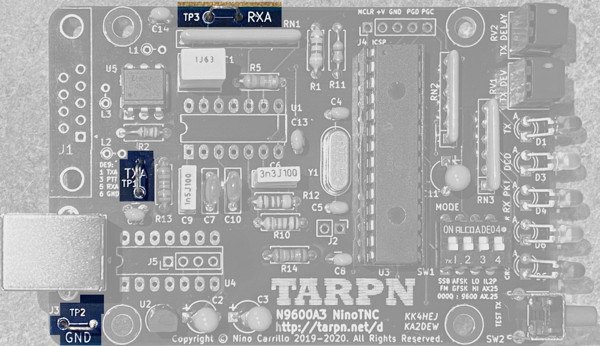 |
33 |
U1 |
MCP6004 quad op-amp
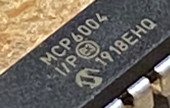 |
Install the MCP6004 quad op-amp Integrated Circuit without a socket.
The pins will have to be bent a little to fit. See step 30.
Since the PCB is now rather crowded, and since the pin bending isn't really obvious,
I recommend test-fitting the IC on the back of the PCB, and then when you get the pins bent as needed, move around to the front of
the PCB and insert the op-amp where it needs to be.
This is a quad-package op-amp (operational amplifier) used to buffer the receive AF data signal from the radio and to condition and buffer the transmit AF data signal to the radio.
The quad op-amp has 4 separate amplifier sections. 3 of these are used in the transmit AF signal processing. 1 in the receive.
Make sure the half-moon shaped end lines up with the PCB as shown in the photos.
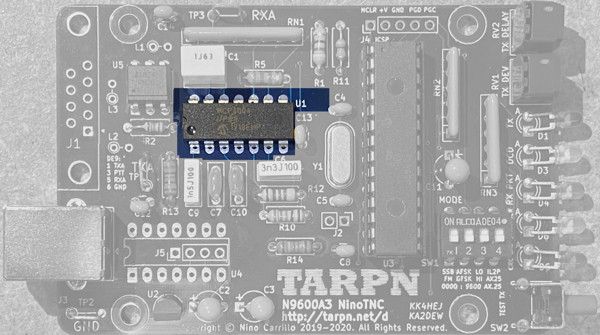 |
34 |
U4 |
MCP2221 or MCP2221A USB interface chip
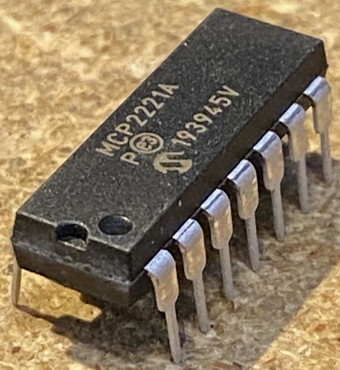 |
Install the MCP2221A USB-serial interface Integrated Circuit without a socket.
Make sure the half-moon shaped end aims toward the USB-B socket.
Note the extra header pins, J5, underneath where U4 MCP2221 is installed.
These pins are for an optional header to be used if the TNC will have a TTL interface and separate 5v source.
This could be handy for an embedded project where USB interconnect would be inefficient.
If you intend to use a TTL interface to the NinoTNC, don't install U4.
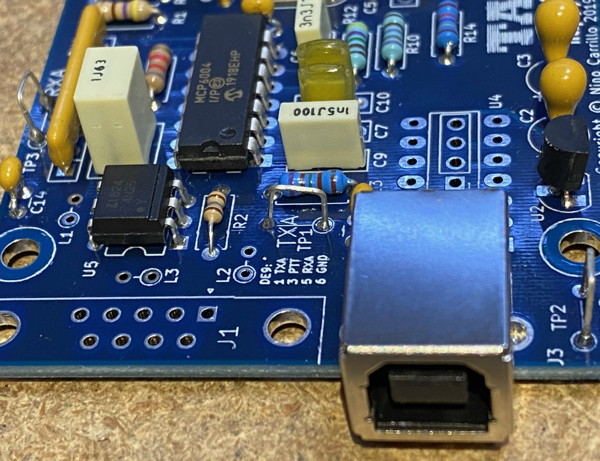 |
35 |
J1 |
DE9 connector 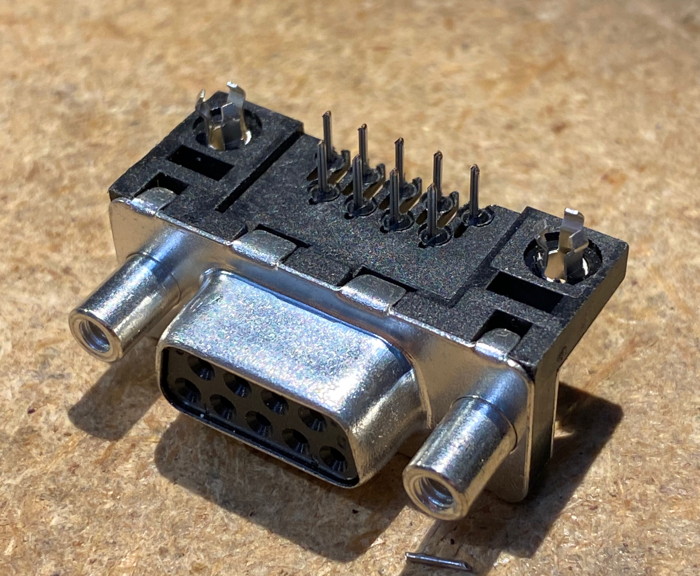 |
This connector is the interface to the transceiver from the NinoTNC.
PTT, TXA data, RXA data, and ground are connected to pins 1, 5, 3 and 6 respectively.
Solder a center pin first, then squeeze the connector into the board and then reheat the center pin.
Now solder the remaining 8 pins and then the two outer fingers in 3 places each.
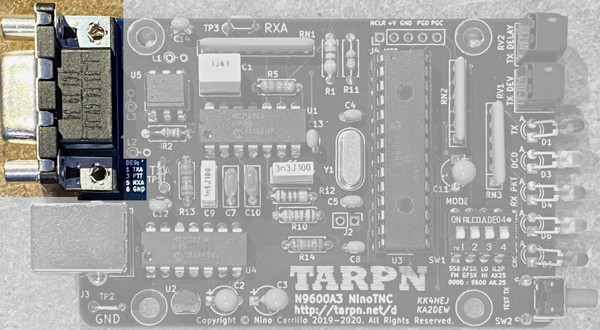 |
Note |
L1, L2, L3 |
Ferrite Bead Choke support
|
There is room on the board for 3 ferrite beads. The pads for the beads are labelled L1, L2, L3 but they are shorted
by a pre-existing trace on the board. Before using one or more of these locations, use a fine-bladed knife to cut the pre-existing trace.
Having the ability to install ferrites at these locations would be important if the NinoTNC were seen to reset itself when the connected transmitter is keyed up or if buzzing were present in the transmit audio. |
Test #3 -- Op Amp
This procedure will show that the op-amp is soldered in correctly and that the support components for the transmit and receive audio paths are installed.
Test Proecedure:-
Set all four switches to off.
- Set the two potentiometers such that the arrows on the yellow screwdriver cross are pointed down toward the PCB.
You may need a magifier to see the arrows.
Click on the photo below to enlarge.
Down toward the PCB is the "middle position" on each potentiometer.
- Attach USB-A to USB-B cable to a powered USB-A socket.
- Plug the USB-B plug into the NinoTNC and observe the LEDs.
- Observe the LEDs flowing left and then right across the left hand four LEDs.
- Press the TEST-TX switch for a second or so, and observe the TX LED illuminating.
With firmware 2.45 and later the orange LED, D6, will light as well.
- When the TEST-TX switch is released, the TX LED should go out.
The TX LED will blink back on briefly.
- Power off and then back on the TNC by pulling and replugging the USB.
- Now use a clip-lead to jumper between the TXA scope loop and the RXA scope loop.
- Press the TEST-TX switch for a second and observe the red TX LED illuminating (with or without D6 orange LED).
- Now release the TEST-TX switch and observe the other LEDs.
Ignore D6, the orange LED, for the moment as it's behavior is different for old vs new firmware.
It should illuminate at some point during this test, regardless.
- If the board is assembled correctly, the red TX LED should go off.
then both the red TX LED and the yellow DCD LEDs should flash briefly,
and then the green RX-PKT LEDs should illumniate for a short period.
- The most common mistakes in assembly are badly soldered parts.
Inspect for solder flowing around the wire and the pad.
Some solder should flow up through the board around the pin and that should be visible on any resistor.
Look for backwards resistor packages.

Test #4 -- USB Driver
This test procedure shows that you are getting a USB connection from the computer to the NinoTNC.
It does not test that the CPU is working or that the USB can talk to it.
You will need a computer whose OS lets you see when a new USB device is attached.
Test Proecedure for MSWindows XP, 7, Vista, 8, 10:
- Attach the USB-A end of a USB cable to a computer and set up the computer to show you what USB devices are attached.
- Find and open the Device Manager on MSWindows.
It is available from Start and then right-click on "Computer" and then click on Device Manager.
Note that this varies by MSWindows OS version.
If you can generate screen shots detailing this, I would love to have copies and make a separate web page per OS version.
- Attach the USB-B end of the USB cable to the NinoTNC.
- Observe that a new item appears in the Device Manager.
It may be in "Other" or in "Universal System Bus Controllers" and it will have the text "MCP-2221 USB-I2C/UART Combo".
That's the NinoTNC.
- If the computer offers to get a driver for this unit, let it download it from the Internet.
The good news about using an obscure combo USB chip is that nobody is cloning it, yet, or that Microchip is defending itself from.
- TBD.. at this point I want to demonstrate how you can use a MSWindows built in terminal program to send a command to the NinoTNC and get it to respond.
I don't have that description yet.
Hopefully you have a program which can talk to a KISS TNC and demonstrate that this works.
An important detail you may need is that the NinoTNC appears to be a 57600baud serial connection.
See the
Operations page for more info